Zugeschnitten: Ein Besuch bei der BLS-Polsterei
Das Stoffmuster mit den grünen Punkten auf dem blauschwarzen Hintergrund auf unseren Sitzen gehört zur BLS wie der Lötschberg. Unsere Fahrgäste sind damit bestens vertraut, weniger bekannt ist hingegen die dafür zuständige BLS-Polsterei. Ein Blick hinter die Kulissen offenbart eine moderne «Wundermaschine», effiziente Digitalisierungsprozesse und auch etwas Pizzeria-Stimmung.
«Das Material wird über ein Vakuum im Laufband angesogen» erklärt Aeberhard nur eines von zahlreichen Merkmalen der Sonderanfertigung, welche die BLS im Mai 2024 angeschafft hat und welche seither die Effizienz der BLS-Innenausstattung beträchtlich erhöht hat.
Moment mal, BLS-Innenausstattung? Richtig gelesen, damit unsere Fahrgäste bequem reisen können, verfügt die BLS über eine eigene Sattlerei und Polsterei. Von der Textil- und Lederverarbeitung der Sitze für sämtliche Züge der BLS-Flotte, über Bodenbeläge bis hin zu mechanischen und pneumatischen Revisionen von Führerstandsitzen werden in der Werkstätte in Bönigen zahlreiche Dienstleistungen erbracht. Obwohl der CNC-Cutter das neue Prunkstück ist, prägen also auch zahlreiche Nähmaschinen, Stoff- und Materiallager oder Werkbänke die Räumlichkeiten vor Ort. Für die Aufarbeitung und Neuanfertigung der Bestuhlung in den Zügen ist bei der BLS ein Team von acht Personen zuständig.
Herausforderung Führerstandstuhl
Für Aeberhards Team ist jedoch nicht nur der Komfort der Fahrgäste wichtig, sondern auch jener der Lokführerinnen und Lokführer. Denn der vielleicht wichtigste – ganz sicher aber der meistbenutzte – Sitz in einem Zug ist der Führerstandstuhl. Entsprechend hoch ist auch dessen Verschleiss. Das ist aber nicht die einzige Herausforderung bei der Revision der Führerstandssitze: Unterschiedliche Grössen bei den jeweiligen Zugmodellen, eine spezifische Pneumatik und Mechanik prägen die Reparaturen.
Vielfältige Kundschaft: BLS, SOB oder auch das Militär
Während der CNC-Cutter im Hintergrund gerade Material für den Glacier Express zuschneidet, erklärt Aeberhard, dass andere Bahnunternehmen wie die SOB oder MGB ebenfalls zur Kundschaft der BLS-Polsterei zählen und ergänzt überraschend «sogar für die Armee durften wir schon Aufträge wahrnehmen, etwa beim Zuschnitt von Bremsfallschirmtaschen». So ist auch die aktuelle Auslastung sehr hoch. Dies führt dazu, dass für laufende Projekte der BLS – wie dem Refit der Lötschberger-Züge – hin und wieder auf Vorrat produziert wird. So finden sich im Lager vorrätige Sitzhüllen, die jederzeit für den Bezug bereitgemacht werden könnten. Dies ermöglicht eine flexible Reaktion auf externe Kundenbedürfnisse.
Digitalisierung: Effizienzsteigerung und Materialeinsparungen
Entsprechend erfreulich ist die erwähnte Effizienzsteigerung des neuen CNC-Cutters. Konkret wurde früher bei manuellen Schnittarbeiten rund 20 Minuten Arbeitszeit für eine Gummidichtung für Türen aufgewendet, während nun inklusive Vorbereitungszeit in etwa der gleichen Zeit 20 Teile produziert werden.
Digitalisierung: Fehlererkennung und automatische Anordnung
Den wahrscheinlich grössten Effizienzgewinn erreicht die neue Schnittmaschine durch die Digitalisierung des sogenannten Schnittbilds. Wie dieser Prozess funktioniert, erklärt die Fachspezialistin Martina Lengacher aus Aeberhards Team: «Erst fotografieren und digitalisieren wir die gewünschten Muster, die wir später ausschneiden wollen – beispielsweise Ausschnitte für Kopfstützen. Die so generierten Teile werden vom System automatisch möglichst effizient und materialschonend auf die je nach Material unterschiedliche Form projiziert.» Dabei erkennt der Cutter auch bereits allfällige Materialfehler auf dem Leder und platziert die Schnittmuster darum herum. Dies führt neben der Vereinfachung des Prozesses auch zu erheblichen Materialeinsparungen.
Noch bleibt Handarbeit gefragt
Komplett automatisch funktioniert es dann aber doch nicht: Nachdem der Cutter seinen Teil der Arbeit erledigt hat und alle Teile präzis zugeschnitten wurden, entfernt Aeberhard das übriggebliebene Leder. Um die zugeschnittenen Teile einfach vom Laufband zu entfernen, behilft sich Aeberhard ausserdem eines Holzspachtels. Lachend fügt er hinzu, dass – bei aller Digitalisierung – die Erfahrungen vom heimischen Pizzaofen dafür schon hilfreich seien.
Der Cutter im Einsatz
Im Video erhältst du Einblicke in die Digitalisierung eines Schnittbilds auf jenem Leder, welches für BLS-Kopf- und Armstützen eingesetzt wird. Dazu siehst du den Cutter bei Schnittarbeiten für das Material des Glacier Express.
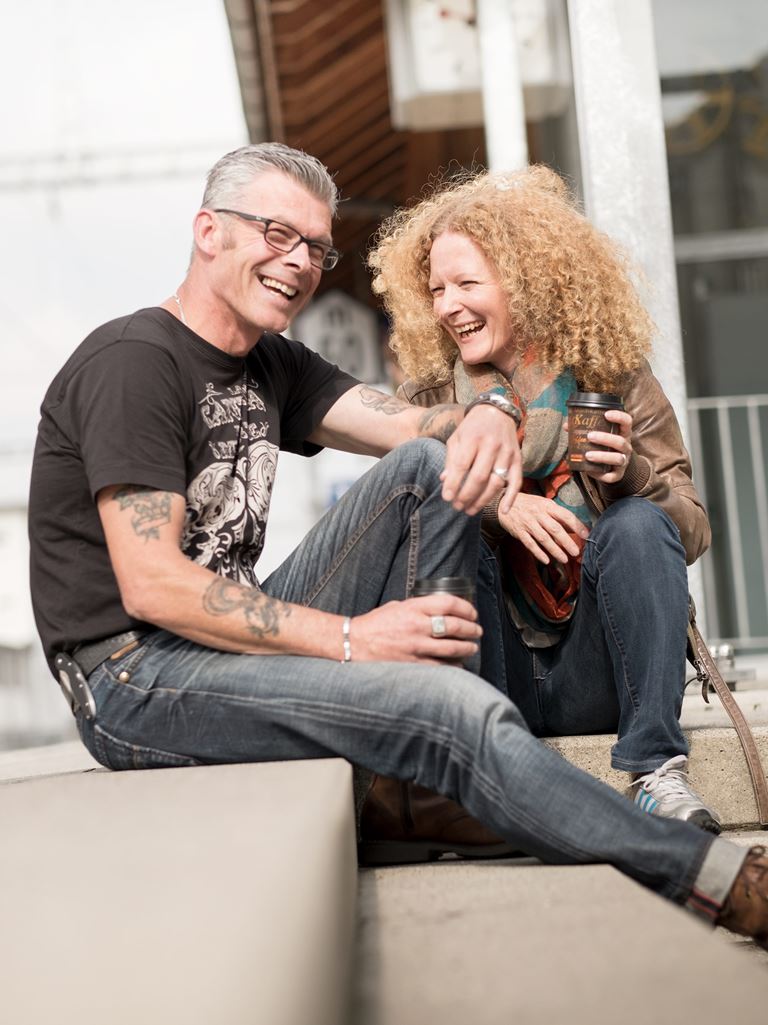
«Verschiedene Fachpersonen mit unterschiedlichen Ausbildungen arbeiten in der Innenausstattung der BLS (Innendekoration, Leder & Textil, Sattlerei). Aber auch Quereinsteiger:innen sind in René Aeberhards Team tätig. Wie in vielen handwerklichen Berufen kämpft die BLS auch hier um Fachkräfte.
Interessiert du dich für das Aufgabengebiet, dann melde dich.»
Von Colin Cuvit